How to Maximise Waste Heat Recovery in Industrial Processes
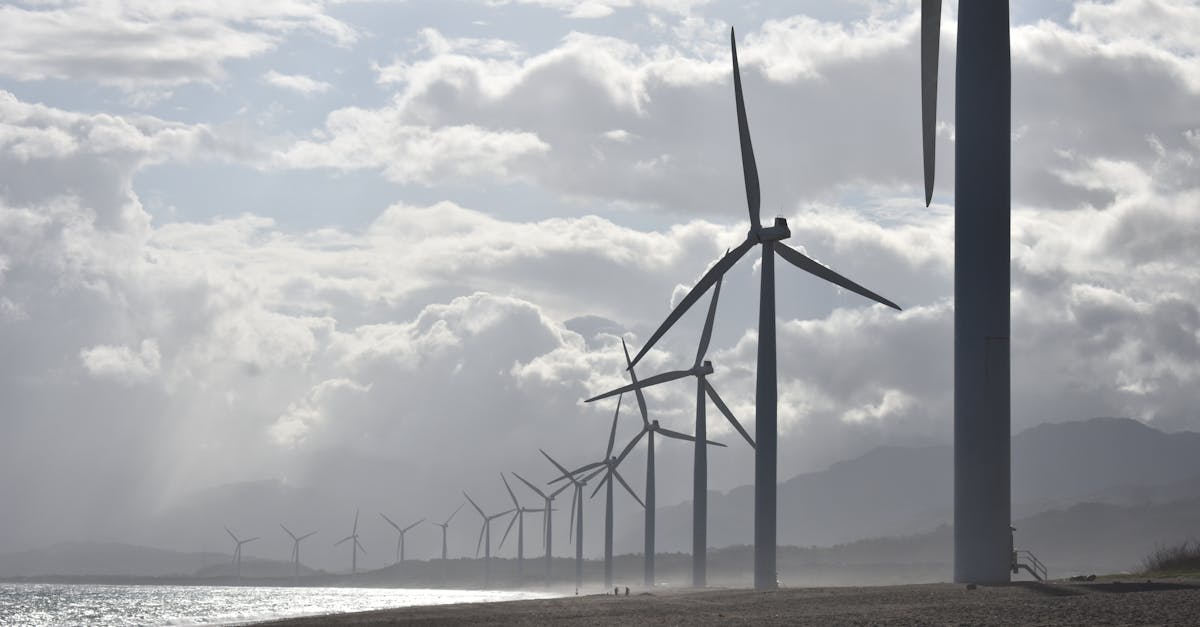
Optimising Existing Processes
Existing industrial processes often hold untapped potential for waste heat recovery. By conducting a thorough assessment, facilities can identify areas where heat losses occur. Upgrading insulation, utilising heat exchangers or enhancing equipment efficiency can significantly reduce the amount of heat released into the environment. Implementing these measures not only maximises energy retention but also lowers costs associated with energy consumption.
The integration of waste heat recovery systems can further optimise energy usage. Retrofitting existing machinery or utilising combined heat and power (CHP) systems allows plants to harness waste heat for heating or electricity generation. Even using recovered heat for preheating process fluids or space heating can lead to considerable energy savings. These optimisations result in enhanced operational efficiency while contributing to sustainability goals within the industrial sector.
Improving Efficiency and Reducing Waste
Enhancing the efficiency of industrial processes often involves a thorough assessment of energy utilisation. Identifying areas where energy loss occurs can lead to the implementation of system upgrades or modifications. Adjusting operational parameters and equipment configurations plays a vital role in minimising waste heat generation. By optimising these aspects, facilities can reduce their overall energy consumption while improving productivity.
Another effective strategy involves the integration of advanced technologies to capture and reuse waste heat. Upgrading to high-efficiency equipment can significantly diminish the amount of heat wasted in processes. Additionally, employing heat exchangers can allow facilities to recycle heat for use in other processes or heating applications. This not only contributes to reducing costs but also supports environmental sustainability by lowering greenhouse gas emissions.
Monitoring and Measuring Performance
Evaluating the effectiveness of waste heat recovery systems requires robust monitoring techniques. This process involves the installation of sensors and data loggers that capture real-time performance metrics. By tracking parameters such as temperature differentials, flow rates, and energy outputs, facilities can identify opportunities for optimisation and pinpoint inefficiencies. Regular assessments not only ensure compliance with regulations but also facilitate proactive maintenance, ultimately enhancing the longevity of recovery systems.
The establishment of a comprehensive performance database can significantly contribute to informed decision-making. Key metrics should include total recovered heat, energy savings, and carbon footprint reductions. Analysing these indicators over time reveals trends and patterns that inform operational adjustments. Furthermore, benchmarking against industry standards allows companies to understand their position relative to competitors, fostering a culture of continuous improvement in waste heat recovery efforts.
Key Metrics to Track Success
Monitoring key metrics is essential for assessing the effectiveness of waste heat recovery systems. Important indicators include the temperature differential of captured heat, the volume of heat recovered over time, and the efficiency of the recovery equipment. By tracking these metrics, companies can identify areas for improvement and ensure that their systems are operating optimally. Regular data collection facilitates informed decision-making and highlights the return on investment realised through waste heat recovery initiatives.
Additionally, energy savings play a vital role in measuring success. Calculating the reduction in energy consumption and subsequent cost savings provides concrete evidence of the system's impact. It is beneficial to benchmark these figures against industry standards or previous performance to validate progress. Engaging with stakeholders to communicate improvements derived from these metrics can foster a culture of sustainability within the organisation and motivate further investments in efficiency enhancements.
Case Studies of Successful Implementation
Industries across various sectors have increasingly embraced waste heat recovery systems, demonstrating tangible benefits. A notable example is a chemical manufacturing plant that employed a heat exchanger to reclaim energy from exhaust gases. This initiative resulted in a 25% reduction in energy consumption and significant cost savings. The recovered heat was redirected to facilitate pre-heating processes, enhancing overall productivity while lowering emissions.
In the food processing sector, a dairy plant implemented a heat recovery system that drew thermal energy from its cooling processes. This innovative approach not only improved energy efficiency but also ensured better temperature control for product consistency. After the system's installation, the facility reported a 30% increase in operational efficiency and a large decrease in water consumption, showcasing the potential for both economic and environmental gains in industrial applications.
RealWorld Examples of Heat Recovery
A notable example of effective heat recovery can be found in the steel industry, specifically at a facility in Sweden. This operation implemented a robust heat recovery system that captures waste heat generated in the production process. The system reuses this captured energy to preheat incoming raw materials, significantly reducing the overall energy consumption and lowering operational costs. This strategy not only minimises waste but also enhances the facility's sustainability profile by decreasing its carbon footprint.
In the food and beverage sector, a brewery in the United Kingdom has successfully utilised heat recovery for its operations. The brewery installed heat exchangers to reclaim steam energy from the brewing process. This recovered heat is then employed to warm water used in subsequent washing processes. As a result, the brewery reported substantial savings on energy expenses and improved its overall efficiency. This implementation showcases how even traditional sectors can harness heat recovery to achieve better resource management and operational performance.
FAQS
What is waste heat recovery in industrial processes?
Waste heat recovery refers to the process of capturing and reusing heat that would otherwise be lost during industrial operations. This recovered heat can be used for various applications, such as heating water, generating steam, or even powering turbines for electricity generation.
How can existing processes be optimised for better waste heat recovery?
Existing processes can be optimised by conducting energy audits, upgrading equipment to more efficient models, and implementing heat exchangers. Regular maintenance and operator training can also enhance system efficiency and reduce waste.
What metrics should be monitored to measure the success of waste heat recovery initiatives?
Key metrics include the percentage of waste heat recovered, the reduction in energy consumption, overall system efficiency, and the cost savings achieved. Tracking these metrics helps assess the effectiveness of heat recovery systems.
Can you provide examples of successful waste heat recovery implementations?
Yes, case studies have shown successful implementations in various industries, such as a food processing plant that reused heat to preheat incoming water, resulting in significant energy savings, and a chemical manufacturing facility that integrated a heat recovery system to improve overall efficiency.
What are some common challenges faced when implementing waste heat recovery systems?
Common challenges include high initial investment costs, the complexity of retrofitting existing systems, and the need for ongoing maintenance and monitoring. Additionally, the variability of heat sources can complicate recovery efforts.
Related Links
Why Conduct Energy Audits and AssessmentsWhat are the Benefits of Renewable Energy Integration
Roundup of Best Practices for Energy Audits
Review of the Latest Technologies in Waste Heat Recovery
7 Effective Strategies for Process Optimisation
Historical Overview of Energy Management Systems in Industry
Why Waste Heat Recovery is Essential for Industries