Review of the Latest Technologies in Waste Heat Recovery
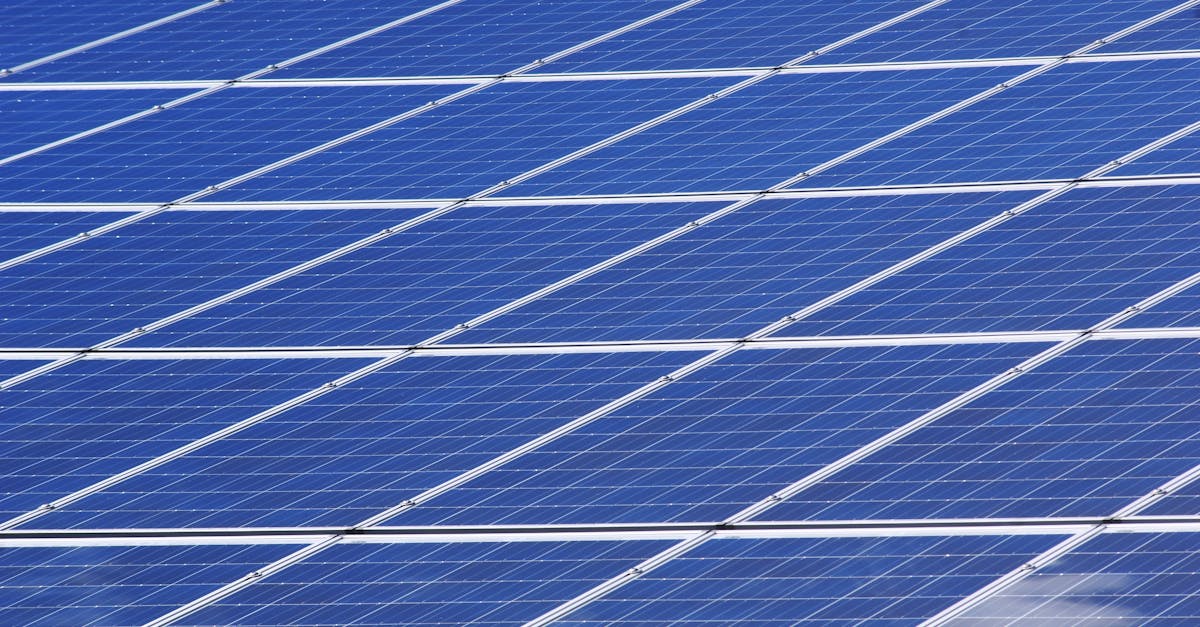
Combined Heat and Power (CHP) Systems
CHP systems play a significant role in improving energy efficiency by simultaneously generating electricity and useful heat from the same energy source. This dual output is particularly advantageous in settings like industrial plants, hospitals, and university campuses, where both electricity and thermal energy are necessary. By utilising waste heat that would typically be lost in conventional power generation methods, these systems optimise fuel consumption and reduce greenhouse gas emissions. Their design can vary significantly, incorporating different technologies such as gas turbines, steam engines, or reciprocating engines, adapting to the specific energy needs of different facilities.
The integration of CHP systems into existing energy infrastructures can lead to substantial cost savings over time. These systems often lead to reduced operational expenses by minimising energy purchases from the grid. With advancements in technology, many modern CHP installations also allow for flexibility in operation, adapting to fluctuating energy demands. Furthermore, the ability to scale these systems according to the capacity requirements makes them suitable for a range of applications, enhancing their appeal as a sustainable energy solution.
Benefits of Integrated Heat and Power Solutions
An integrated approach to heat and power solutions offers numerous advantages for both efficiency and sustainability. By simultaneously generating electricity and useful thermal energy from the same energy source, these systems can significantly reduce energy consumption and lower emissions. The synergy created between the two processes allows for optimal use of fuel, resulting in improved overall system efficiency compared to conventional separate production methods. This integration can lead to substantial cost savings, making these systems an appealing option for facilities aiming to enhance their energy management strategies.
In addition to financial incentives, integrating heat and power promotes resilience in energy supply. These systems can provide critical support during peak demand periods, aiding in reducing the strain on the grid. The ability to harness waste heat for additional power generation further strengthens their appeal, especially in industries with high thermal outputs. As organisations increasingly focus on reducing their carbon footprint, these solutions align with broader sustainability goals while ensuring reliable energy availability.
Advances in Material Technology
Recent developments in materials science have led to the creation of advanced thermoelectric materials, which play a crucial role in enhancing heat recovery systems. These materials convert waste heat directly into electricity with improved efficiency, enabling industries to harness energy that would otherwise be lost. By optimising the composition and microstructure of these materials, researchers have significantly increased their thermal and electrical conductivity. This advancement paves the way for more sustainable energy solutions in various industrial applications.
Alongside thermoelectric materials, researchers are also exploring nanostructured materials that offer remarkable improvements in heat transfer capabilities. The utilisation of nanoparticles within conventional heat exchangers has demonstrated potential for boosting performance by increasing surface area and enhancing thermal conductivity. This innovation not only improves the overall efficiency of heat recovery systems but also allows for compact designs, making implementation in space-constrained environments more feasible. These strides in material technology are crucial to advancing waste heat recovery methods across multiple sectors.
Innovative Materials Enhancing Heat Recovery Efficiency
Recent advancements in material technology have led to the development of enhanced thermoelectric materials. These materials exhibit improved thermoelectric conversion efficiency, facilitating more effective capture and utilisation of waste heat. Researchers have focused on optimising materials such as bismuth telluride and skutterudites, which are renowned for their capability to convert temperature differences into electrical energy. Utilising these innovative materials can significantly increase the energy output from waste heat recovery systems and reduce reliance on fossil fuels.
In addition to thermoelectric materials, phase change materials (PCMs) have emerged as a promising solution in heat recovery applications. PCMs absorb and release thermal energy during phase transitions, allowing for efficient thermal management in various processes. Their ability to store excess heat during periods of high production and release it during low-demand periods enhances overall system efficiency. Integrating these materials into waste heat recovery systems can optimise energy usage and promote sustainability across different industries.
Case Studies of Successful Implementations
Several notable projects have demonstrated the effectiveness of waste heat recovery systems across various industries. In a large automotive manufacturing facility, the integration of a Combined Heat and Power (CHP) system allowed for the capturing of excess heat generated during production processes. This recovered energy not only provided a substantial reduction in operating costs but also resulted in significant decreases in carbon emissions, showcasing a successful balance between economic and environmental benefits.
In another instance, a food processing plant implemented an innovative heat recovery solution by utilising exhaust gases from their furnaces. By installing heat exchangers, the facility was able to transfer waste heat to pre-heat water for cleaning processes. This initiative not only enhanced overall energy efficiency but also demonstrated the potential for considerable savings in energy consumption, underlining the practicality and advantages of adopting waste heat recovery technologies in industrial settings.
RealWorld Applications Demonstrating Effectiveness
In various industries, waste heat recovery systems have proven their worth through practical applications, contributing significantly to energy efficiency. For instance, many manufacturing plants have successfully integrated Combined Heat and Power (CHP) systems. These installations not only capture excess heat generated during production processes but also convert it into usable electricity and steam for heating. The result is a significant reduction in energy costs, demonstrating the systems’ dual functionality and economic viability.
Another notable example is the utilisation of innovative materials in heat exchangers within the automotive sector. Advances in materials science have led to the development of lightweight, highly conductive composites that optimise heat recovery from exhaust emissions. These advancements have enabled manufacturers to improve the overall thermal efficiency of vehicles, thereby reducing fuel consumption and greenhouse gas emissions. Such implementations highlight the transformative potential of adopting cutting-edge technologies in waste heat recovery across diverse sectors.
FAQS
What are waste heat recovery technologies?
Waste heat recovery technologies are systems that capture and reuse thermal energy that would otherwise be lost during industrial processes, power generation, or other operations, improving overall energy efficiency.
How do Combined Heat and Power (CHP) systems work?
Combined Heat and Power (CHP) systems generate electricity and useful heat simultaneously from the same energy source, optimising the energy produced and reducing waste.
What are the benefits of integrated heat and power solutions?
Integrated heat and power solutions offer numerous benefits, including increased energy efficiency, reduced energy costs, lower greenhouse gas emissions, and enhanced energy security.
What types of materials are used in innovative heat recovery technologies?
Innovative materials used in heat recovery technologies include high-performance alloys, ceramics, and advanced composites that improve thermal conductivity and resistance to degradation at high temperatures.
Can you provide examples of successful waste heat recovery implementations?
Yes, numerous case studies demonstrate successful waste heat recovery implementations, including applications in manufacturing plants, power stations, and district heating systems, where significant energy savings and emissions reductions have been achieved.
Related Links
Roundup of Best Practices for Energy Audits7 Effective Strategies for Process Optimisation
Historical Overview of Energy Management Systems in Industry
Why Waste Heat Recovery is Essential for Industries
Why Conduct Energy Audits and Assessments
How to Maximise Waste Heat Recovery in Industrial Processes