How to Maximise Waste Heat Recovery in Industrial Processes
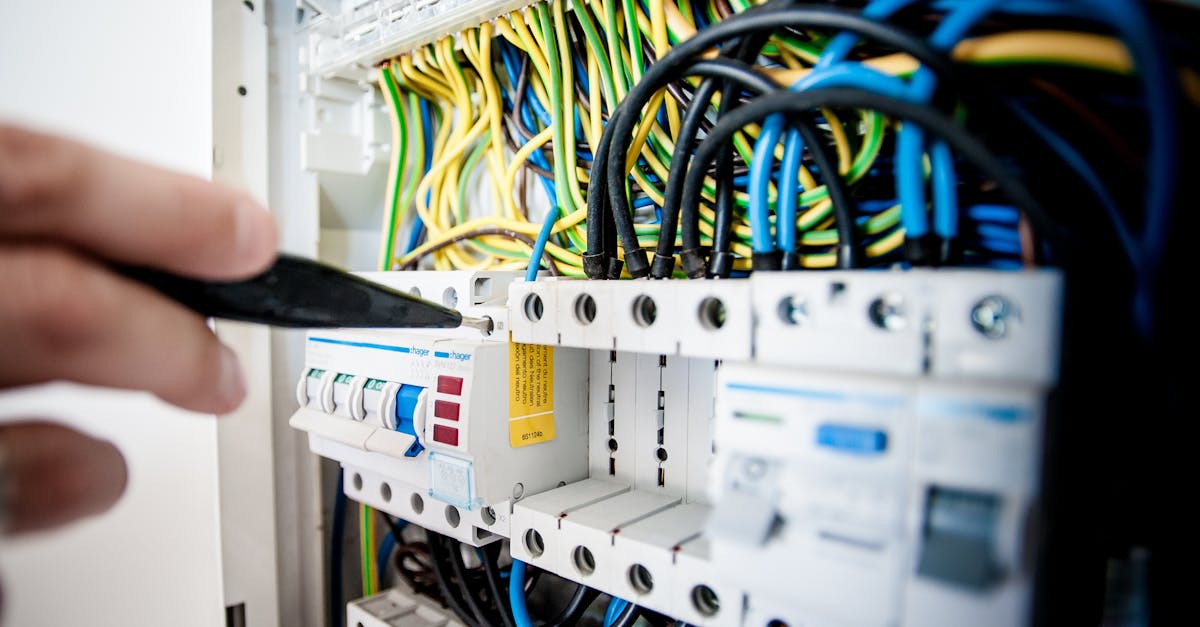
Designing an Effective Recovery System
A well-structured recovery system is crucial in maximising the benefits of waste heat. An initial assessment of the industrial process in question allows for understanding specific temperature ranges, heat sources, and the potential for heat reuse. Identifying the primary heat streams and their characteristics enables engineers to select appropriate technologies for recovering heat effectively, such as exchangers, turbines, or thermal storage systems. Critical attention should be paid to the thermal dynamics within the facility, ensuring that the recovery system aligns seamlessly with existing operations to maintain productivity.
In addition to technical selection, the layout and integration of the recovery system within the facility hold significant importance. A strategic design minimizes energy losses during transport through well-insulated piping and optimally placed equipment. Collaborating with different stakeholders, including process engineers and maintenance teams, ensures that any integration challenges are addressed early in the design phase. This collaborative approach promotes a comprehensive understanding of operational constraints and allows for the creation of a tailored solution that maximises energy efficiency while maintaining overall system reliability.
Factors to Consider in System Design
When designing a waste heat recovery system, it is essential to identify the specific sources of waste heat within the industrial process. Understanding the temperature and quantity of waste heat available for recovery allows for the selection of appropriate technologies, such as heat exchangers or heat pumps. It is also important to assess the system's operating conditions, including pressure variations and relevant heat transfer characteristics. This knowledge helps in determining the most efficient way to capture and utilise this energy while ensuring compatibility with existing processes.
The system design must also consider factors such as the desired return on investment and potential environmental impacts. Evaluating the economic feasibility of different recovery methods ensures that the chosen system will be financially viable for the long term. Additionally, incorporating flexibility into the design can accommodate variations in operational demand and prevent overdesign or underutilisation. This adaptability is crucial for maintaining optimal performance and achieving sustainable energy use within the industrial framework.
Implementing Waste Heat Recovery Solutions
Incorporating waste heat recovery solutions requires a strategic approach tailored to the specific needs of the industrial process. Initially, conducting an energy audit can help identify the primary sources of waste heat. This evaluation provides insights into the potential volume of heat available for recovery. Once the sources are determined, selecting the appropriate technology becomes crucial. Options such as heat exchangers, heat pumps, and organic Rankine cycle systems can be assessed based on efficiency, cost, and compatibility with existing processes.
Pilot projects can play a vital role in the integration process, allowing facilities to test the effectiveness of the chosen system on a smaller scale before full implementation. Collaboration with engineering and process teams ensures that the system aligns with operational requirements and regulatory standards. Training staff on the new system is essential for optimal performance. Monitoring tools and sensors should also be deployed to gather data on system efficiency and identify any necessary adjustments. Taking these proactive steps enhances the likelihood of success in implementing heat recovery solutions.
Steps for Successful Integration
Effective integration of waste heat recovery systems into existing industrial processes requires careful planning and execution. Conducting a thorough analysis of current operations helps identify key areas where energy losses occur. This assessment should involve collaboration between engineers, operators, and management to foster a comprehensive understanding of the facility's workflows. Prioritising robust designs that align with operational needs will enhance overall performance.
Once the analysis is complete, begin by establishing clear objectives for the recovery system. Defining success metrics will streamline the integration process. It is vital to ensure that all stakeholders are informed and engaged throughout implementation. Training staff on new technologies and practices guarantees smooth operation and encourages adherence to best maintenance practices. Regular updates and reviews will also play a critical role in addressing any challenges that may arise during the integration phase.
Monitoring and Maintenance of Recovery Systems
Regular monitoring is crucial for the effective operation of waste heat recovery systems. Advanced sensors and data analytics tools should be integrated to track system performance. These technologies aid in detecting inefficiencies or malfunctions before they escalate into significant issues. Routine checks can provide valuable insights into operational parameters and help ensure that the system operates at optimal efficiency.
Scheduled maintenance plays a vital role in prolonging the lifespan of recovery systems. Maintenance tasks should include cleaning heat exchangers and inspecting insulation for damage. This proactive approach not only optimises energy recovery but also minimises unexpected downtime. Developing a comprehensive maintenance schedule tailored to specific operational needs fosters reliability and enhances overall system performance.
Ensuring Longterm Efficiency
Regular monitoring plays a crucial role in maintaining the efficiency of waste heat recovery systems. Implementing an effective monitoring strategy allows for the identification of potential issues before they escalate into significant problems. This often includes the use of sensors to track performance metrics such as temperature, flow rates, and pressure levels. Analysing this data regularly supports timely adjustments and optimisations, ensuring the system operates within its designed parameters.
Additionally, routine maintenance is essential to guard against inefficiencies caused by wear and tear or fouling. Establishing a maintenance schedule for cleaning, inspections, and component replacements can prolong the lifespan of the system and improve its overall performance. Engaging with experienced technicians for maintenance tasks provides assurance that the system remains in optimal condition. Sustainability also benefits from these practices, as they help to minimise energy waste and reduce operational costs over time.
FAQS
What is waste heat recovery?
Waste heat recovery refers to the process of capturing and reusing the excess heat generated during industrial processes, thereby improving energy efficiency and reducing overall energy consumption.
Why is designing an effective recovery system important?
An effective recovery system is crucial as it ensures maximum capture of waste heat, optimises energy usage, and ultimately leads to cost savings and reduced environmental impact.
What factors should be considered in the design of a waste heat recovery system?
Key factors include the type of heat generated, temperature levels, available technologies for recovery, existing equipment compatibility, and the specific energy needs of the facility.
What are the steps for successful integration of waste heat recovery solutions?
Successful integration involves assessing current processes, identifying suitable recovery technologies, designing the system, ensuring proper installation, and training staff for optimal operation.
How can I ensure the long-term efficiency of waste heat recovery systems?
Regular monitoring and maintenance, including performance assessments and timely repairs, as well as adapting the system to any changes in production processes, are essential for maintaining long-term efficiency.
Related Links
What is Process Optimisation in Energy EfficiencyHow to Implement an Effective Energy Management System
Roundup of Best Practices in Renewable Energy Integration
10 Tips for Effective Waste Heat Recovery
Review of Leading Energy Management Software Solutions
The Evolution of Energy Management Systems in Industry
Why is Energy Efficiency Important for Sustainable Development
What are the Benefits of Renewable Energy Integration