What to Consider When Optimising Industrial Processes
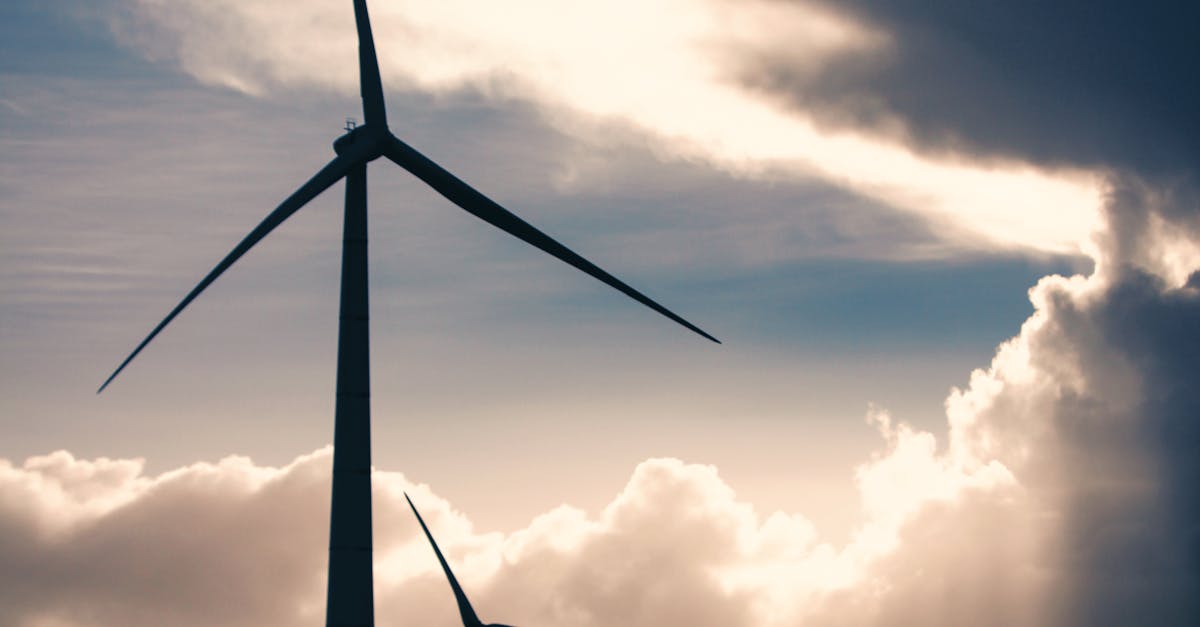
Fostering Employee Training
A well-trained workforce is essential for enhancing the efficiency of industrial processes. Investing in comprehensive training programmes equips employees with the necessary skills and knowledge to understand operational protocols and technological tools. Regular workshops and hands-on training sessions not only boost confidence among staff but also foster an environment of continuous improvement. This commitment to employee development can lead to innovative ideas and solutions that streamline production.
Additionally, embracing a culture of ongoing learning encourages employees to stay updated with industry trends and best practices. Training should focus on various aspects, from technical skills to safety procedures, ensuring that every member of the team is prepared to tackle the challenges of modern industrial operations. Providing opportunities for professional growth can also increase job satisfaction, resulting in lower turnover rates and a more cohesive workforce dedicated to enhancing productivity.
Developing Skills for Process Improvement
Investing in employee training is crucial for enhancing process improvement within industrial settings. Providing staff with the right tools and knowledge can lead to greater efficiency and innovation. Workshops, seminars, and hands-on training sessions can cultivate essential skills among workers. Encouraging a culture of continuous learning allows employees to stay updated with the latest techniques and technologies. This proactive approach not only benefits individual performance but also influences overall operational success.
Encouraging collaboration among team members can further facilitate skill development. By fostering an environment where knowledge sharing is valued, organisations can draw upon diverse perspectives and experiences. Regular team-building exercises and collaborative projects can enhance problem-solving capabilities and creativity. Additionally, mentorship programmes can guide less experienced employees, accelerating their learning curve and integrating their fresh insights into established processes. Investing in these developmental areas can substantially contribute to driving process improvements across the board.
Monitoring Environmental Impact
Understanding the environmental footprint of industrial processes is essential for sustainable operations. Measuring emissions, waste generation, and resource consumption helps organisations identify areas requiring improvement. Regular assessments allow companies to adapt their practices in alignment with both regulatory standards and corporate social responsibility goals, fostering a proactive approach to environmental stewardship.
Incorporating monitoring systems can enhance awareness and promote responsible resource use among employees. Furthermore, leveraging technology, such as real-time data analytics, can provide insights into operational efficiency while highlighting potential environmental impacts. This commitment not only contributes to compliance but also strengthens a company's reputation in a marketplace increasingly driven by eco-conscious consumers.
Assessing Sustainability Practices
Evaluating sustainability practices within industrial processes requires a thorough examination of resource usage and waste management. Companies must analyse their consumption patterns, identifying areas where resources are being over-utilised or wasted. This consideration not only helps in reducing costs but also contributes to a more sustainable operational model. Incorporating renewable energy sources and materials with lower environmental footprints can significantly enhance a company’s sustainability profile.
Another crucial aspect is the assessment of supply chains and their environmental impact. Understanding how raw materials are sourced and the emissions produced during transport reveals opportunities for improvement. Engaging with suppliers who share a commitment to sustainable practices can foster a more eco-friendly approach. Additionally, conducting life cycle assessments allows companies to evaluate the environmental effects of their products from inception to disposal, guiding them towards more sustainable decision-making throughout their operations.
Analyzing Costs
Cost analysis serves as a crucial element in refining industrial processes. Accurate assessment of all expenses associated with production allows companies to identify inefficiencies and areas with the potential for financial savings. Businesses should scrutinise various cost components such as raw materials, labour, and overheads. This detailed examination not only highlights excessive expenditure but also reveals opportunities for negotiation with suppliers and optimising resource allocation.
Effectiveness can be assessed through various methods, including monitoring key performance indicators (KPIs), conducting regular audits, and soliciting employee feedback to identify areas for enhancement.
What are some common areas where financial savings can be identified during cost analysis?
Common areas for financial savings include reducing energy consumption, minimising waste, streamlining supply chain processes, and optimising equipment maintenance schedules.
Why is monitoring environmental impact important in industrial optimisation?
Monitoring environmental impact is important as it helps companies ensure compliance with regulations, reduce their carbon footprint, and improve their overall sustainability, which can enhance their reputation and attract customers.