10 Best Practices for Process Optimisation in Manufacturing
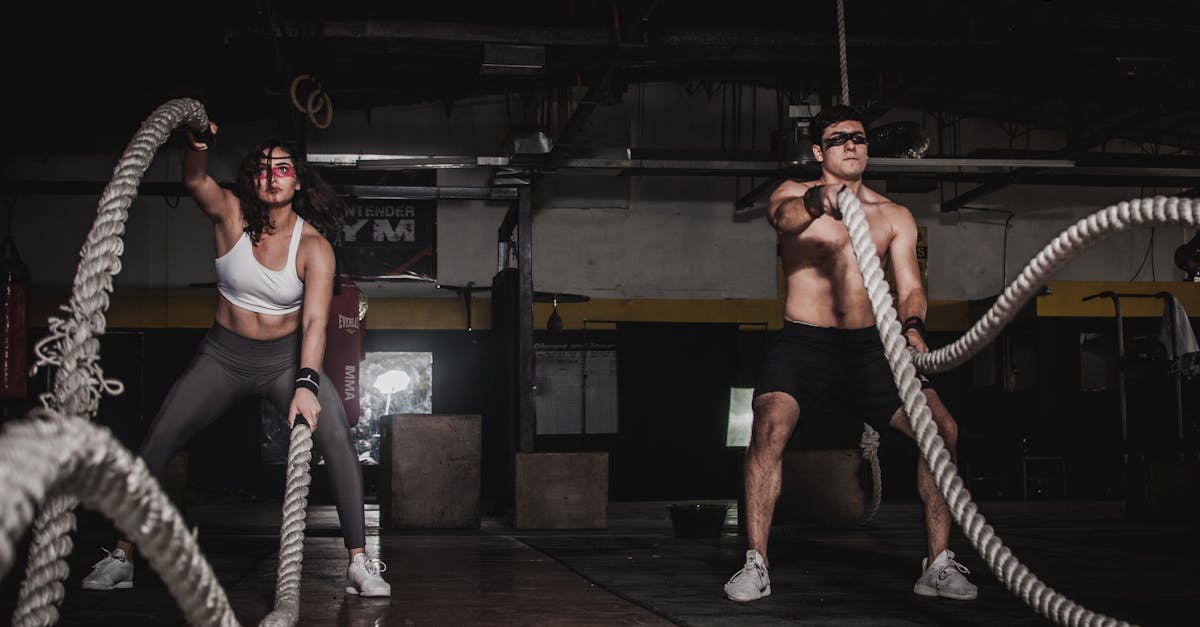
Standardise Procedures
Establishing standardised procedures forms the backbone of an efficient manufacturing operation. Consistency in processes leads to predictable outcomes, reducing variability and minimising errors. When teams follow a unified set of guidelines, it not only streamlines workflows but also enhances time management across various stages of production. Furthermore, standardisation simplifies the training of new employees, enabling them to quickly grasp their roles and responsibilities.
Implementing standard procedures also facilitates easier measurement and analysis of performance. When all team members adhere to the same processes, it becomes straightforward to identify areas that require improvement or adjustment. Gathering data becomes more meaningful as variations can be accurately tracked and attributed to specific practices. This systematic approach ensures that best practices can be consistently applied, fostering a stable foundation for ongoing optimisation efforts.
Creating Detailed Work Instructions
Detailed work instructions play a crucial role in ensuring that manufacturing processes run smoothly and consistently. By providing clear and precise guidelines for each task, operators can perform their duties with confidence. Comprehensive instructions help reduce variability and set a standardised approach, which is essential for maintaining quality control throughout the production line. Visual aids, such as diagrams and photographs, can enhance understanding, making it easier for workers to follow complex procedures.
Regularly reviewing and updating these instructions is essential to adapt to changes in processes or technology. This practice not only ensures that employees have the most current information at their fingertips but also allows for the integration of feedback gained from the workforce. Engaging employees in the development of these work instructions fosters a sense of ownership and encourages adherence to the established guidelines, ultimately leading to improved efficiency and product quality.
Monitor Performance Continuously
In today's fast-paced manufacturing environment, continuous performance monitoring plays a crucial role in optimising processes. By regularly assessing key performance indicators (KPIs), organisations can identify inefficiencies and areas needing improvement. This approach allows for quick adjustments to be made, minimising downtime and maximising productivity. Incorporating automated monitoring systems can enhance the accuracy of data collection, making it easier to analyse trends over time.
Real-time data analytics is essential for effective performance monitoring. It enables manufacturers to respond to issues as they arise rather than relying on historical data that may no longer reflect current conditions. Implementing such systems empowers teams to make informed decisions, driving efficiency and ensuring quality control. Ultimately, a proactive approach to performance monitoring fosters a robust operational environment, aligning with organisational goals.
Utilising RealTime Data Analytics
The integration of real-time data analytics within manufacturing processes allows for immediate insights into operational performance. By harnessing data from various stages of production, companies can identify inefficiencies and areas for improvement. This analytical approach enables quick responses to issues, minimising downtime and maximising productivity.
Additionally, leveraging advanced analytics tools paves the way for informed decision-making. Manufacturers can track key performance indicators (KPIs) in real-time, allowing for a more agile strategy in managing resources and workflows. This proactive stance not only enhances overall efficiency but also drives down costs while maintaining product quality.
Foster a Culture of Continuous Improvement
Establishing an environment where employees feel empowered to suggest improvements can significantly enhance manufacturing processes. This approach cultivates engagement and motivates team members to be actively involved in identifying inefficiencies. When workers understand that their insights are valuable, it promotes a sense of ownership and responsibility over their tasks, leading to innovative solutions and streamlined operations.
Creating structured feedback mechanisms can facilitate ongoing dialogue between employees and management. Regularly scheduled meetings or brainstorming sessions encourage the sharing of ideas and experiences. By recognising and rewarding contributions towards process optimisation, organisations reinforce the importance of continuous improvement. This fosters loyalty and enhances both individual and collective performance, ultimately driving the organisation towards its strategic goals.
Encouraging Ongoing Training and Development
Investing in ongoing training ensures that employees remain skilled and knowledgeable about the latest manufacturing techniques and technologies. Regular workshops and seminars can expose workers to innovative practices and tools that enhance efficiency. Employers should also consider tailoring training programmes to meet specific needs within the organisation, promoting relevance and effectiveness.
Creating a supportive environment for learning fosters engagement and motivation among staff members. Managers can encourage employees to take ownership of their professional development by providing access to various educational resources, such as online courses or industry conferences. Recognition of achievements in training can further stimulate a positive culture, reinforcing the value of continuous learning in manufacturing operations.
FAQS
What is process optimisation in manufacturing?
Process optimisation in manufacturing refers to the systematic approach of enhancing production processes to improve efficiency, reduce waste, and increase productivity.
Why is it important to standardise procedures in manufacturing?
Standardising procedures ensures consistency across operations, reduces errors, and streamlines training, leading to improved efficiency and quality in manufacturing processes.
How can real-time data analytics benefit manufacturing performance?
Real-time data analytics allows manufacturers to monitor processes continuously, identify bottlenecks, and make informed decisions quickly, ultimately improving overall operational efficiency.
What role does a culture of continuous improvement play in manufacturing?
A culture of continuous improvement encourages employees at all levels to seek out and propose enhancements to processes, fostering innovation and adaptability in a competitive market.
How can ongoing training and development impact process optimisation?
Ongoing training and development ensure that employees are equipped with the latest skills and knowledge, enabling them to contribute effectively to process improvements and adapt to new technologies.
Related Links
Review of the Latest Waste Heat Recovery TechnologiesThe History of Energy Management Systems in Industry
Roundup of Top Energy Management Systems for Industrial Use
Why Energy Audits are Essential for Industrial Operations
Why Renewable Energy Integration is Crucial for Energy Efficiency
What to Consider for Successful Process Optimisation in Industry