What to Consider for Successful Process Optimisation in Industry
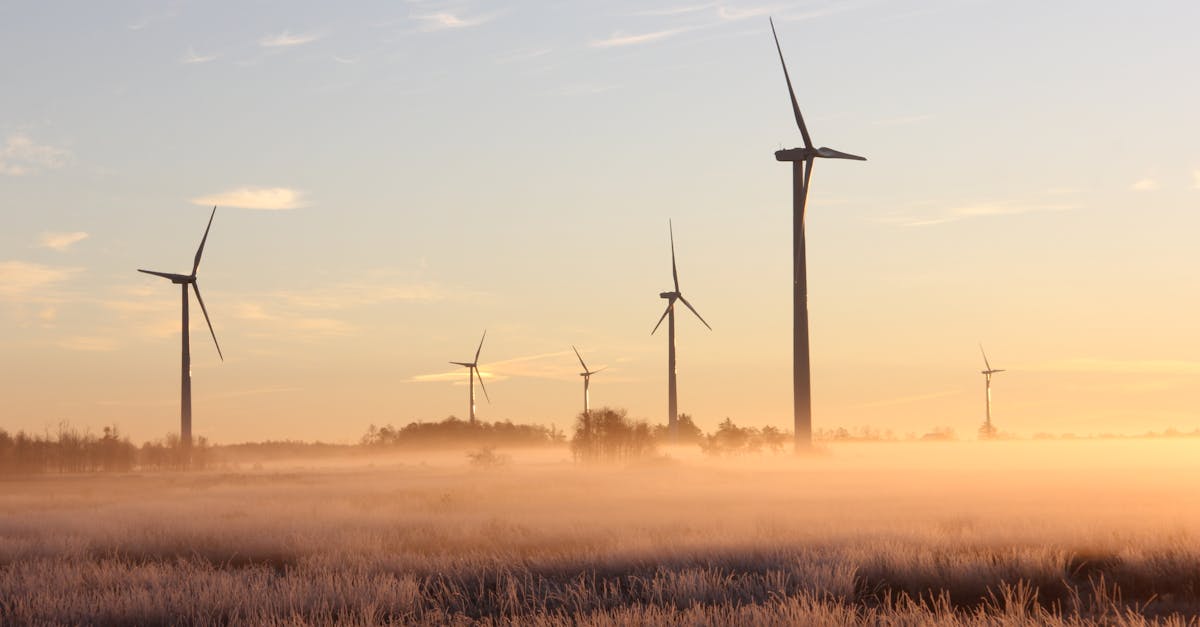
Data Analysis and Metrics
In today's competitive landscape, robust data analysis is paramount for identifying inefficiencies and opportunities within industrial processes. Companies can gain insights into their operations by collecting and examining relevant data, enabling informed decisions aimed at process optimisation. Metrics serve as vital indicators, allowing organisations to assess performance and benchmark against industry standards. A systematic approach to data analysis facilitates the detection of trends and patterns that may not be immediately evident, ultimately guiding strategic improvements.
Utilising the right metrics is essential when measuring the success of optimisation initiatives. Key Performance Indicators (KPIs) tailored to specific goals can effectively illustrate progress and highlight areas requiring attention. For instance, metrics related to productivity, quality, and cost-efficiency provide a comprehensive view of performance. An ongoing review of these metrics ensures that companies remain agile, allowing them to adapt and refine their strategies as new data emerges. By prioritising data analysis and clearly defined metrics, organisations can establish a strong foundation for continuous improvement and long-term success.
Measuring Success through Key Performance Indicators
npoint inefficiencies. By fostering a culture of continuous improvement, organisations can create a more responsive and agile working environment that adapts to changing demands.
On the other hand, Six Sigma emphasises reducing variation and improving quality in processes. It employs statistical methods to identify defects and implement solutions for consistency. The DMAIC framework—Defining, Measuring, Analyzing, Improving, and Controlling—provides a structured approach for problem-solving. Both methodologies, when adopted together, offer a powerful combination for organisational transformation, enhancing operational efficiency and ultimately delivering greater customer satisfaction.
Training and Development
Investing in training and development is crucial for fostering a culture that prioritises process optimisation. Providing employees with the necessary skills not only empowers them to perform their tasks effectively but also enhances overall productivity. Tailored training programmes can help staff understand new technologies, methodologies, and best practices essential for streamlining operations. Such initiatives encourage proactive problem-solving and innovation among team members.
Moreover, upskilling employees contributes to job satisfaction and retention. When individuals feel supported in their professional growth, they are more likely to remain engaged and committed to their roles. A well-structured development programme serves to align individual goals with organisational objectives, creating an environment where everyone works towards common outcomes. This synergy catalyses the success of process optimisation efforts across the industry.Copyright © Climate Energy. All rights reserved.
Upskilling Employees for Enhanced Performance
The workforce plays a crucial role in the success of process optimisation initiatives. Investing in employee training ensures that team members are equipped with the latest skills relevant to their roles. Fostering a culture of continuous learning not only empowers individuals but also drives overall productivity. When employees understand the intricacies of new processes and tools, they can contribute to improvements more effectively.
Offering targeted training sessions helps bridge the skills gap. Learning opportunities can take various forms, including workshops, online courses, or mentorship programmes. Engaging employees in hands-on training allows them to appreciate the practical applications of their skills. Facilitating an environment where knowledge is readily shared promotes collaboration and innovation, ultimately leading to enhanced performance throughout the organisation.
FAQS
What is process optimisation in an industrial context?
Process optimisation refers to the systematic approach of improving a process's efficiency and effectiveness in an industrial setting, aiming to enhance productivity, reduce costs, and improve quality.
How can data analysis contribute to process optimisation?
Data analysis helps identify inefficiencies, monitor performance, and provide insights into process dynamics, enabling informed decision-making and targeted improvements.
What are Key Performance Indicators (KPIs), and why are they important?
Key Performance Indicators are measurable values that demonstrate how effectively a company is achieving its key business objectives. They are crucial for tracking progress and measuring the success of process optimisation efforts.
What methodologies are commonly used for continuous improvement?
Popular continuous improvement methodologies include Lean, which focuses on waste reduction, and Six Sigma, which aims to improve quality by identifying and removing causes of defects.
How can employee training and development impact process optimisation?
Upskilling employees enhances their ability to contribute effectively to process improvements, fostering a culture of continuous improvement and ensuring that the workforce is equipped to implement new strategies and technologies.
Related Links
Why Renewable Energy Integration is Crucial for Energy EfficiencyWhat to Know About Waste Heat Recovery Technologies
Roundup of Top Energy Management Systems for Industrial Use
Review of the Latest Waste Heat Recovery Technologies
10 Best Practices for Process Optimisation in Manufacturing
The History of Energy Management Systems in Industry
Why Energy Audits are Essential for Industrial Operations