Review of the Latest Waste Heat Recovery Technologies
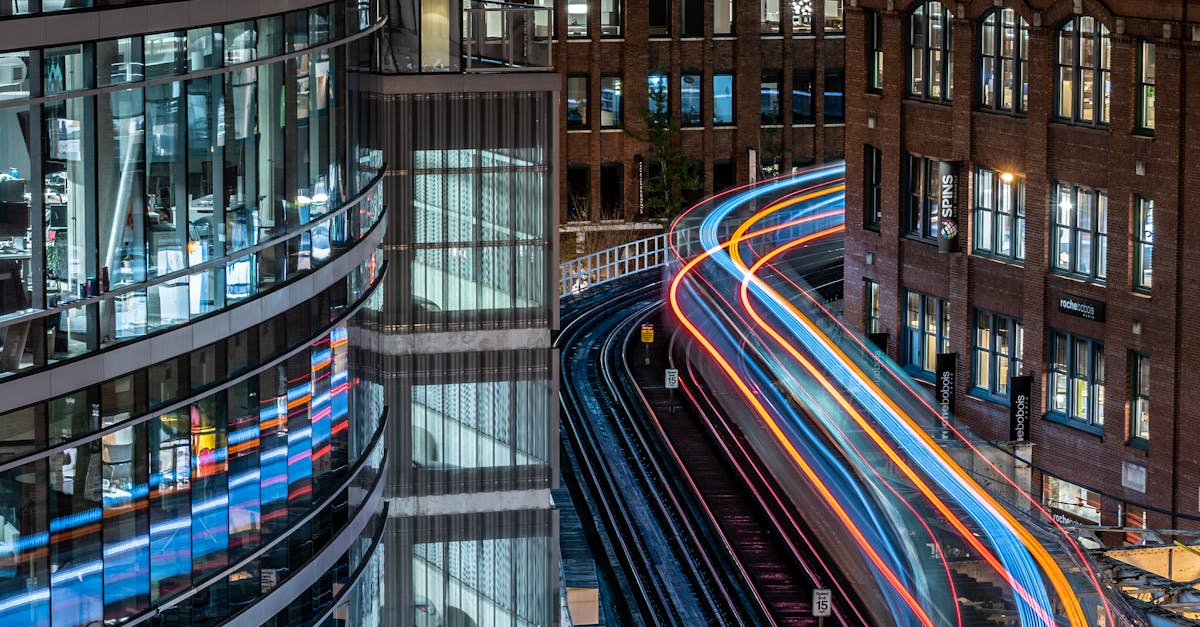
Waste Heat Boilers
Waste heat boilers capture and utilise waste gases or heat from industrial processes to generate steam or hot water. These systems are most effective in industries with high-temperature exhaust, such as power generation and metal processing. By recycling waste heat, these boilers improve overall energy efficiency and reduce environmental impact. Their design typically incorporates specialised heat exchanger surfaces that optimise thermal recovery while maintaining safety and operational reliability.
In terms of operation, waste heat boilers often employ advanced control systems to monitor temperature and pressure conditions. This precision helps to maximise heat recovery and streamline energy conversion. Many models feature modular designs that allow for easy integration with existing processes. This adaptability makes waste heat boilers a practical choice for factories aiming to enhance sustainability while lowering operational costs. The increasing emphasis on green technology continues to drive innovations in waste heat boiler design and functionality.
Design and Operational Features
Waste heat boilers are intricately designed to optimise the recovery of energy from high-temperature flue gases. These systems can operate at varying pressure levels and are constructed from materials capable of withstanding extreme temperatures and corrosive environments. The incorporation of advanced heat exchangers enhances thermal efficiency, allowing for maximised energy capture. Furthermore, many units feature modular designs, facilitating easy maintenance and integration within existing industrial setups.
Operational efficiency is paramount in these systems. Automated controls enable precise regulation of flow rates and temperature, ensuring optimal performance under fluctuating operational conditions. The implementation of advanced monitoring systems aids in real-time analysis, identifying potential inefficiencies or faults promptly. These features collectively contribute to a reliable and effective method for harnessing waste energy, significantly reducing overall operational costs and environmental impact.
Thermoelectric Generators
These devices harness temperature differences to generate electricity through the Seebeck effect. They comprise two different materials that create a potential difference when subjected to varying temperatures. The efficiency of thermoelectric generators depends largely on the materials used, particularly those with high thermoelectric performance. This technology is suitable for applications where waste heat is prevalent, such as in industrial processes, vehicle exhaust systems, and even renewable energy systems.
Recent advances focus on improving the performance and sustainability of these devices. Researchers are exploring various advanced materials, including nanostructured and layered composites, to enhance efficiency. Innovations such as flexible thermoelectric materials and nanocrystalline structures showcase significant potential for improved thermal-to-electrical conversion. These developments not only aim to increase power output but also to widen the operational temperature range, making thermoelectric generators more adaptable to diverse applications across multiple industries.
How They Convert Heat to Electricity
Thermoelectric generators (TEGs) utilise materials that exhibit the thermoelectric effect, enabling them to convert temperature differences directly into electric voltage. When one side of a thermoelectric material is heated while the other remains cool, charge carriers within the material migrate from the hot side to the cooler side. This movement of charge carriers creates an electric current, which can then be harnessed for power generation. The efficiency of this conversion process largely depends on the properties of the materials used and the magnitude of the temperature gradient applied.
The applications of TEGs vary widely, with niches in both industrial and residential settings. They are particularly advantageous in scenarios where waste heat is prevalent yet difficult to capture through conventional means. By integrating these generators into systems such as exhaust or flue gas streams, energy that would otherwise be lost can be effectively converted into usable electricity. Despite ongoing challenges related to improving efficiency and material durability, advancements in thermoelectric technology continue to reveal significant potential for enhancing energy recovery efforts across multiple sectors.
Advanced Materials in Heat Recovery
Developments in advanced materials have significantly impacted the efficiency of heat recovery systems. Researchers are increasingly focused on enhancing the thermal conductivity of materials to optimise heat exchange processes. Novel composites and nanomaterials, including graphene and carbon nanotubes, are being explored for their remarkable thermal properties. These materials not only improve the effectiveness of heat recovery methods but also contribute to weight reduction and increased durability of systems.
In addition to better heat transfer capabilities, advanced materials are being developed to withstand extreme temperature fluctuations and corrosive environments. Coatings designed to enhance resistance to oxidation and wear are essential in extending the lifespan of heat recovery equipment. Furthermore, the integration of these materials into existing infrastructures allows for retrofitting opportunities in various industries. Innovative approaches continue to emerge, highlighting the pivotal role that materials science plays in advancing the field of waste heat recovery.
Innovations Enhancing Performance
Recent developments in advanced materials have significantly improved the efficiency of waste heat recovery systems. The use of nanostructured materials is becoming increasingly popular due to their superior thermal conductivity. These materials facilitate enhanced heat absorption, enabling systems to operate at higher temperatures without compromising structural integrity. Furthermore, coatings that increase emissivity are now being applied to surfaces, allowing for greater heat transfer and minimising losses.
Another notable advancement lies in the integration of smart sensors and IoT technology. These innovations enable real-time monitoring and management of heat recovery systems, optimising performance based on actual operational conditions. Data collected through these sensors can inform predictive maintenance, ensuring that systems run smoothly and efficiently. This not only extends the lifespan of the equipment but also maximises the recovery potential of waste heat, leading to better overall system performance.
FAQS
What are waste heat recovery technologies?
Waste heat recovery technologies are systems designed to capture and reuse excess heat that is generated during industrial processes or power generation, allowing for increased energy efficiency and reduced environmental impact.
How do waste heat boilers work?
Waste heat boilers operate by capturing waste heat from exhaust gases and converting it into steam or hot water, which can then be used for various applications such as electricity generation or process heating.
What are thermoelectric generators?
Thermoelectric generators are devices that convert temperature differences directly into electrical energy using the Seebeck effect, making them an effective solution for converting waste heat into usable electricity.
What role do advanced materials play in heat recovery technologies?
Advanced materials enhance the performance of heat recovery systems by improving thermal conductivity, resistance to corrosion, and durability, which ultimately leads to better efficiency and longevity of the technologies.
Are there any environmental benefits associated with waste heat recovery technologies?
Yes, waste heat recovery technologies help reduce greenhouse gas emissions by lowering fuel consumption and enhancing overall energy efficiency, contributing to more sustainable industrial practices.
Related Links
Roundup of Top Energy Management Systems for Industrial Use10 Best Practices for Process Optimisation in Manufacturing
The History of Energy Management Systems in Industry
Why Energy Audits are Essential for Industrial Operations
Why Renewable Energy Integration is Crucial for Energy Efficiency
What to Consider for Successful Process Optimisation in Industry
What to Know About Waste Heat Recovery Technologies
How to Implement Effective Energy Management Systems in Industrial Settings