How to Implement Effective Energy Management Systems in Industrial Settings
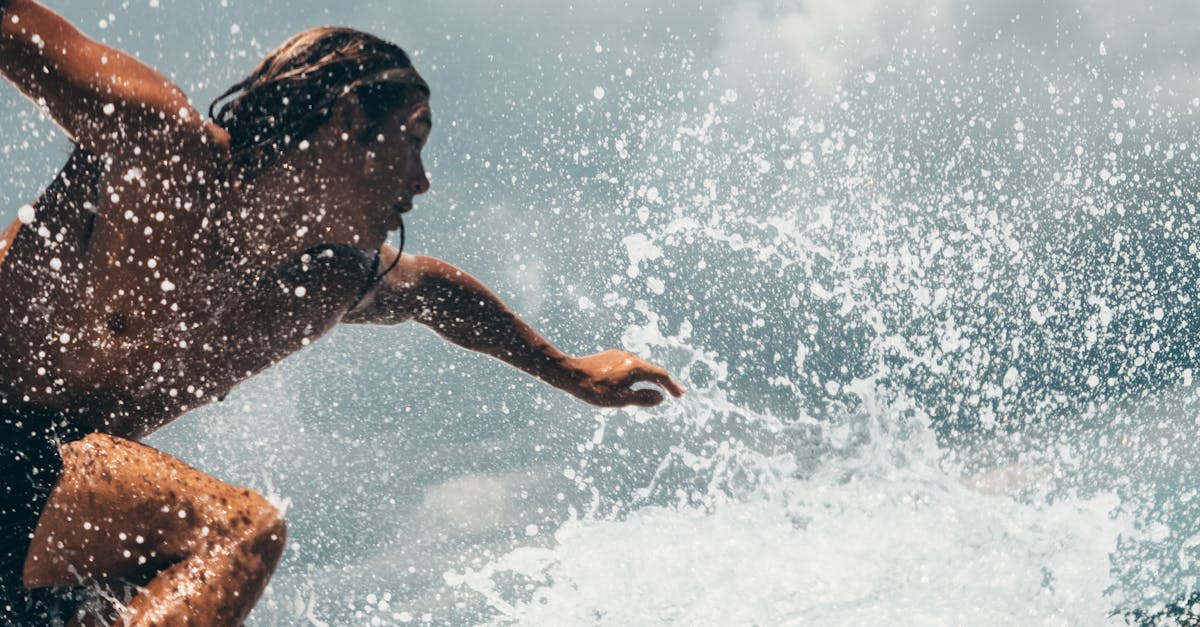
Implementing Energy Monitoring Tools
The integration of energy monitoring tools is crucial for enhancing efficiency within industrial settings. These tools enable organisations to collect and analyse real-time data regarding energy consumption patterns. By employing smart meters and advanced sensors, facilities can gain insights into energy usage across various machinery and processes. This facilitates the identification of peak consumption times and potential areas of waste, offering a clearer picture of how energy is allocated and utilised.
Selecting appropriate monitoring technologies is essential for effective energy management. Various systems are available, ranging from basic consumption tracking to sophisticated analytics platforms capable of providing predictive insights. It is important to choose solutions that align with the specific needs of the operation, ensuring scalability and adaptability as technology evolves. Implementing these technologies not only enhances data visibility but also empowers teams to make informed decisions regarding energy efficiency initiatives.
Types of Monitoring Technologies
Monitoring technologies play a crucial role in the effective management of energy in industrial settings. Various tools are available to track energy usage, each with its unique features and benefits. Smart meters allow for real-time monitoring and can collect data on energy consumption patterns. Sensors and data loggers provide insights into specific equipment performance, while software solutions can analyse data to identify trends and anomalies in energy usage.
Another category of monitoring tools includes energy management software, which integrates with existing systems to offer comprehensive data analysis. This software can generate reports, helping managers visualise energy consumption and pinpoint areas for improvement. Additionally, enterprise-level systems provide a broad view of energy use across multiple sites, facilitating company-wide energy optimisation strategies. The selection of suitable monitoring technologies is foundational to developing a robust energy management programme.
Identifying Energy Efficiency Opportunities
Recognising potential areas for energy efficiency within an industrial setting involves a thorough assessment of existing operational processes. This assessment typically includes analysing energy consumption patterns, understanding peak usage times, and identifying equipment inefficiencies. Employees working on the ground can provide valuable insights based on their daily interactions with machinery and systems. Their expertise often highlights unexpected sources of energy waste, such as equipment left running during non-productive hours or suboptimal settings leading to excess power consumption.
A comprehensive review of operational processes can unveil significant opportunities for improvement. This might involve evaluating the age and condition of machinery, as older equipment is often less efficient than newer models designed with energy-saving technologies. Additionally, implementing a strategy for regular maintenance can prevent energy loss caused by wear and tear. Considering options such as retrofitting existing machines with energy-efficient components or reallocating resources based on usage data can lead to substantial energy savings.
Reviewing Operational Processes
A thorough examination of operational processes is essential for uncovering inefficiencies in energy usage. This involves analysing workflows, equipment utilisation, and energy consumption patterns. Assessing each step in a production line or service delivery can reveal opportunities for optimisation. Engaging team members in this review can provide valuable insights, as they often have firsthand knowledge of the nuances of daily operations.
Data gathered from energy monitoring tools can be instrumental in this assessment. This information helps to identify which machines consume the most energy and whether they operate at peak efficiency. Understanding these dynamics allows for targeted interventions. Implementation of best practices can lead to substantial reductions in energy consumption while maintaining productivity levels.
Establishing an Action Plan
Creating a structured action plan involves outlining clear objectives and defining specific steps to achieve energy efficiency goals. This plan should prioritise initiatives based on cost-effectiveness and potential energy savings. In this phase, engaging stakeholders from various departments is crucial, as their insights can help identify the necessary resources and encourage a collective commitment to the energy management strategy.
Once the objectives are set, timelines and responsibilities must be established to ensure accountability. Assigning tasks to team members allows for a systematic approach to implementing energy-efficient practices. Continuous monitoring and evaluation of the action plan is essential to track progress and make adjustments as needed. This iterative process enables organisations to stay on course and adapt to changing circumstances, fostering a culture of sustainability over time.
Prioritising Energy Efficiency Projects
Energy efficiency projects should be assessed based on their potential return on investment and the impact on overall energy consumption. A systematic approach to evaluation can determine which initiatives will yield the most significant savings. Factors such as implementation costs, payback periods, and energy savings should play a role in the decision-making process. This analysis can help identify quick wins alongside longer-term projects, ensuring a balanced portfolio of initiatives.
Stakeholder engagement is essential when prioritising projects. Involving employees and management can enhance understanding and commitment to proposed changes. Establishing clear communication channels allows for the sharing of ideas and feedback. Additionally, setting specific targets for energy reduction can motivate teams and create a sense of accountability. By aligning projects with organisational goals, businesses can ensure that energy efficiency efforts are not only effective but also integral to their broader strategy.
FAQS
What are energy management systems (EMS) and why are they important?
Energy management systems (EMS) are structured frameworks that help organisations monitor, control, and optimise their energy consumption. They are important because they can lead to significant cost savings, increased energy efficiency, and reduced environmental impact.
What types of energy monitoring tools are available for industrial settings?
There are various energy monitoring tools available, including smart meters, energy management software, and IoT-based sensors. These tools help track real-time energy usage, identify trends, and facilitate data analysis.
How can operational processes be reviewed to identify energy efficiency opportunities?
Reviewing operational processes involves analysing the workflow, machinery usage, and energy consumption patterns. This can be done through energy audits, performance assessments, and employee feedback to pinpoint areas where efficiency can be improved.
What factors should be considered when prioritising energy efficiency projects?
When prioritising energy efficiency projects, consider factors such as potential cost savings, return on investment, alignment with organisational goals, ease of implementation, and the environmental impact of the changes.
How can organisations ensure the successful implementation of an energy management system?
Successful implementation of an energy management system can be ensured by securing management commitment, involving staff at all levels, providing training, setting clear objectives, and regularly reviewing and updating the action plan based on performance metrics.
Related Links
What to Know About Waste Heat Recovery TechnologiesHow to Conduct Comprehensive Energy Audits and Assessments
Roundup of Top Energy Management Systems for Industrial Use
Review of the Latest Waste Heat Recovery Technologies
10 Best Practices for Process Optimisation in Manufacturing
The History of Energy Management Systems in Industry
Why Energy Audits are Essential for Industrial Operations